Flame treating is a sophisticated process involving the use of controlled heat to alter the properties of materials, particularly metals and plastics. This method, pivotal in industries such as manufacturing and automotive, relies heavily on profile burners—specialized equipment designed for precise heat application. The importance of controlled heat in various industries cannot be understated; it is crucial for enhancing adhesion, durability, and overall quality of products. In this comprehensive guide, we will traverse the intricacies of flame treating and profile burners, providing insights into the science, applications, benefits, process steps, and case studies surrounding this fascinating technology.
The Science Behind Flame Treating

Flame treating centers around fundamental principles of heat transfer, chemistry, and material science. The role of temperature and time is crucial—different materials require varying degrees of heat and exposure duration to manifest changes. By applying controlled heat, the surface properties of materials are altered, allowing for improved adhesion of coatings and enhanced durability. The alteration occurs at a molecular level, affecting the material’s behavior and interaction with other substances. Understanding these principles is essential, as it underpins the efficiency and effectiveness of this procedure, allowing for meticulous control over material transformations.
Profile Burners: What Are They?
Profile burners are paramount in flame treating, acting as the linchpin in applying controlled heat. These burners come in various types, each designed to cater to specific needs and materials. The essence of profile burners lies in their ability to provide precision in heat application, thereby ensuring uniform treatment of materials. They are constructed to offer consistent, adjustable patterns, allowing for customization according to the material being treated. The meticulous engineering behind profile burners paves the way for optimal performance and results in these processes.
Applications of Flame Treating
The applications of flame treating are extensive and diverse. It is a cornerstone in industries like manufacturing, automotive, and aerospace, contributing significantly to product development and enhancement. In manufacturing, it’s instrumental in preparing surfaces for bonding, while in the automotive sector, it’s pivotal for enhancing the durability of components. These real-world applications, often done by professionals such as Flynn Burner Corporation, underscore the importance of treating in delivering products that meet stringent quality and performance standards. The versatility of this process makes it an indispensable tool in various industrial applications, offering solutions to myriad challenges.
Benefits of Flame Treating

Flame treating stands out among other treatment methods for its myriad benefits. It offers enhanced material adhesion, improved durability, and elevated quality of products. The environmental benefits and cost-effectiveness make it a preferred choice for industries striving for sustainable solutions. The use of profile burners in treating facilitates a reduction in waste and energy consumption, contributing to eco-friendly manufacturing processes. These benefits, coupled with the versatility and efficiency of this process, render it a revolutionary technique in material treatment.
Key Components of Profile Burners
Profile burners are composed of several key components, including burners, controls, and sensors. Each component plays a vital role in ensuring precise heat control and application. The burners generate the flame, controls regulate the flame intensity and duration, and sensors monitor the temperature and adjust the flame accordingly. Advancements in technology have led to the development of highly sophisticated profile burners, enabling unparalleled accuracy and consistency in treating processes.
Flame Treating Process Steps
The process of flame treating with profile burners involves a series of meticulous steps, each crucial for achieving optimal results. Safety precautions and best practices are integral parts of the process, ensuring the well-being of operators and the integrity of the treated materials. The role of operators is paramount—they monitor and adjust the flame treating conditions, making decisions based on the material’s response to heat. Following the correct process steps and adhering to safety guidelines is crucial for successful treating outcomes.
Controlling Heat for Consistency
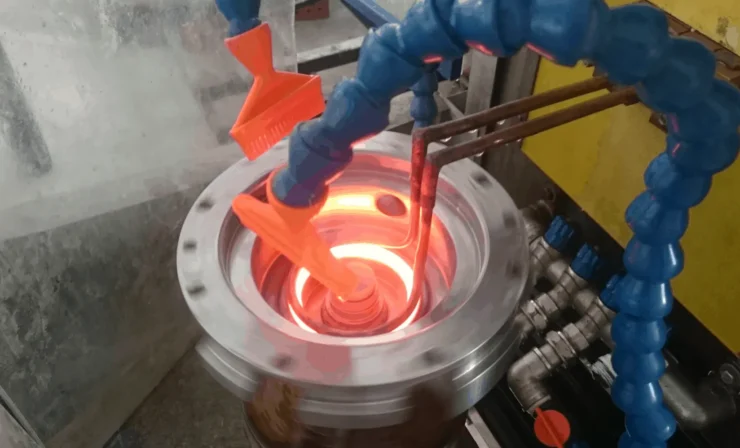
Profile burners facilitate consistent heat application, a vital aspect of flame treating. Temperature monitoring and regulation techniques are employed to maintain uniform heat, ensuring consistent treatment of materials. Quality control is imperative in this context, with stringent checks in place to verify the uniformity and adequacy of heat applied. Achieving consistency in heat application is central to realizing the full potential of flame treating, providing industries with reliable solutions for material enhancement.
Achieving Customized Results
The adaptability of profile burners enables the achievement of customized treatments, allowing adjustments to be made for different materials and products. This flexibility is essential for catering to the diverse needs of various industries, ensuring that each material is treated under optimal conditions. Examples of tailored flame treatments abound, illustrating the capability of profile burners to deliver customized solutions, enhancing the functionality and performance of a wide range of products.
Flame Treating vs. Other Heat Treatment Methods
When juxtaposed with other heat treatment methods, flame treating exhibits unique advantages and limitations. It stands out for its precision, versatility, and efficiency, offering solutions that are tailored to specific material needs. Guidance on choosing the right method is crucial, as it influences the overall outcome of the material treatment. The choice between flame treating and alternative methods hinges on the specific requirements of the application, with each method having its distinct merits.
Case Studies and Success Stories
Several case studies exemplify the remarkable results achieved with flame treating and profile burners. These success stories, complete with before-and-after comparisons and testimonials, underscore the transformative impact of flame treating on materials and products. These real-world examples serve as a testament to the efficacy of flame treating, providing insights into the practical applications and benefits of this innovative technology.
Conclusion and Future Trends
In conclusion, flame treating with profile burners is a revolutionary technique, enabling the alteration of material properties through controlled heat. The key takeaways from this guide include the science behind flame treating, the role of profile burners, the diverse applications, and the benefits of this method. The future trends in flame treating technology are promising, with continual advancements paving the way for more sophisticated and efficient solutions. The exploration of controlled heat with profile burners offers boundless possibilities, encouraging industries to delve deeper into the potential of flame treating.